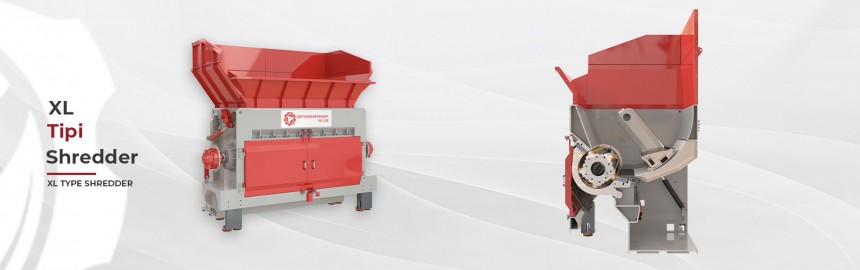
SINGLE-ROTOR SHREDDER XL
SHD XL220-XL280 -XL350
Smart and Flexible Control Systems
The integrated ABB PLC system in Shredder XL adapts to changes in material flow, allowing easy optimization of slide and rotor settings. The recipe system enables material-specific settings to be saved and quickly applied for recurring tasks. All control panels are designed and manufactured at our facilities in Turkey.
Optimal Cutting Gap Achieved with Adjustable Counter Knives
The coordination between the cutting knife and counter knife plays a key role in determining material throughput and the quality of the shredding process. To ensure a consistently precise cutting gap despite natural wear, the counter knives in this series are both manually adjustable and reversible. This ensures efficient energy use, reduces wear-related expenses, and greatly extends the knife’s overall lifespan through optimal cutting geometry.
Flat-Edge Knife Rotor Designed for Demanding Applications
Our innovative design features replaceable rotating knives and holder sets, ensuring ease of maintenance and replacement while significantly extending the rotor's lifespan. Unlike traditional systems, our rotating knife design is not directly attached to the rotor, preventing cutting impact and reducing wear on the rotor itself. With the new flat-edge knife design, specifically engineered for professional-grade processing of RDF (Refuse-Derived Fuel) and municipal solid waste, materials are effectively shredded using short and robust cutting edges. This advanced design ensures consistent cutting performance and exceptional durability, even when dealing with the most challenging waste streams. Tailored to meet the demanding requirements of waste management applications, the knife sizes, quantities, and rotor drive systems are customized for the specific material being processed, delivering superior efficiency and reliability in industrial-scale operations.
Advanced Rotor Engineered for Tough Applications
Our customers frequently rate the flat-edge rotor as one of the top performers in shredding. Featuring short, robust flat-edge knives, it optimizes material intake and cutting efficiency. The flat-edge rotor excels in delivering high throughput while minimizing energy consumption, reducing thermal stress, and significantly lowering wear-related costs. This design is particularly well-suited for challenging materials such as RDF (Refuse-Derived Fuel) and municipal solid waste, offering exceptional durability and consistent performance.
Durable and Quick-Maintenance Cartridge Rotor Design for RDF Processing
One of the biggest challenges in RDF (Refuse-Derived Fuel) processing is having a cutting system that can withstand unexpected metal contaminants. Our new cartridge rotor design ensures maximum resistance against such foreign materials, providing uninterrupted operation and enhanced durability.
The modular cartridge system allows for quick and easy blade replacement. In case of blade damage, only the damaged cartridge needs to be replaced, eliminating the need to disassemble the entire rotor and ensuring minimal downtime. This feature significantly reduces maintenance time while improving overall operational efficiency.
Unlike traditional rotor systems, this design prevents cutting impacts from directly affecting the rotor body, minimizing wear and extending the rotor’s lifespan. The reinforced cutting edges effectively shred even the toughest and most abrasive materials found in RDF streams, ensuring consistent and reliable cutting performance.
Optimized to withstand the harsh conditions of RDF processing, this innovative rotor design offers quick maintenance capabilities and long-term durability, making it a highly efficient solution for industrial waste management applications.
Enhanced Material Flow for Demanding Applications
The XL model features a unique swinging pusher mechanism, specially designed for processing RDF (Refuse-Derived Fuel) and municipal waste. Unlike traditional horizontal pushers, this mechanism oscillates in a swing-like motion, working with gravity to guide materials toward the rotor naturally. The optimized chamber design supports this motion, compressing materials efficiently between the pusher and rotor. This innovative system ensures effective shredding, reduces energy consumption, and minimizes wear, making it ideal for large-scale waste processing with high performance and durability..
Maximum Accessibility for Easy Maintenance
The shredder XL is designed to maximize accessibility and streamline maintenance processes. The hydraulically operated screen basket tilts downward, enabling quick and effortless access for screen replacement and rotor knife maintenance. Additionally, the hydraulic rear maintenance door provides direct access to the shredder’s interior, ensuring convenient inspection and servicing. These features not only improve rotor accessibility but also significantly simplify maintenance operations, minimizing downtime and enhancing operational efficiency.
Flexible Drive Options with Distinct Advantages
The XL shredder offers two distinct drive options, each with unique advantages. The belt-pulley reducer system is a cost-effective solution ideal for standard shredding applications. It is low-maintenance, energy-efficient, and provides a smooth start, reducing stress on the motor and rotor. This system is particularly suited for operations prioritizing simplicity and efficiency. On the other hand, the hydro-motor drive system is designed for more demanding tasks. It delivers high torque and precision control, making it perfect for processing tough materials. This system also offers better durability and shock absorption, ensuring reliable performance under heavy-duty conditions. These features provide flexibility and adaptability for a wide range of operational requirements.
Vibration-Reducing Machine Feet
Compact and durable machine feet made from hard rubber eliminate the need for anchoring the machine to the floor, allowing flexible and convenient installation. These feet effectively absorb and reduce disruptive vibrations, minimizing their impact on the surrounding environment.
SHREDDER XL